GEAR HOBBING MACHINE RETROFIT
BACKGROUND:
• Legacy hardware of 840c with limited service Legacy hardware of 840c with limited service with limited service
• Legacy hardware with obsolete Legacy hardware with obsolete obsoletespare
• Machine in good mechanical condition Machine in good mechanical condition
• Auto loader hardware not functional Auto loader hardware not functional not functional
• Due to maintenance problem no predictable Due to maintenance problem no predictable output
WORK DONE:
• Reverse engineering of machine Reverse engineering of machine engineering of machine
• Selection of correct automation hardware Selection of correct automation hardware
• Adaptation Adaptationof new motors of new motors of new motors
• Electrical Electricaldesign, control design, control design, controlcabinet cabinet cabinet& field wiring field wiring field wiring
• PLCprogram development along with safety program development along with safety
interlocks interlocks
• Cycles & User intuitive screens development Cycles & User intuitive screens development
• CNC configuration and calibration CNC configuration and calibration ration and calibration
• Axis tuning, B, Axis tuning, B,C &Z–Axes coupling s coupling s coupling
• Spur & Helical Gears Spur & Helical Gears prove out prove out prove out
CUSTOMER GAIN:
• Autoloader fully operational Autoloader fully operational
• Predictable production Predictable production redictable production
• Quick retrofit as compare to long delivery of new ma Quick retrofit as compare to long delivery of new machine etrofit as compare to long delivery of new machine
• 30% cost for retrofit as compare to 30% cost for retrofit as compare to for retrofit as compare tonew machine new machine new machine
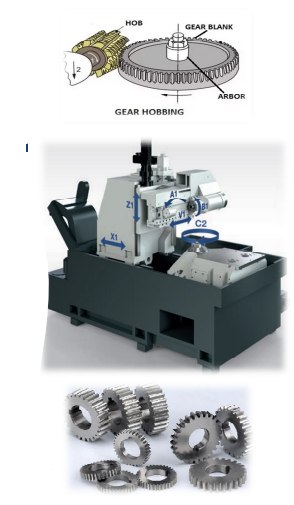
STAMA flat milling
Automation for a legacy 840C controllerfromSiemensAndcreated a new panel
Project details:
Problem Statement
There was no support on existing 840C legacy controller from
Siemens Expensive spares, No Support from OEM, No documentation with
machine
Twin Spindle ATC logic
Solution Provided
Selection of Automation components along with required option bits
Motor Mounting and Field cables routing New Panel Wiring AND ATC Logic
Machine Configuration, PLC Interlocks, Motor Tuning.
Machine Details
Twin Spindle
X, Y, Z Linear Axes with Linear Scale
A11, A22 Rotatory axes
Magazine Axis
New System Details
NCU 710.3 , OP12 TCU, OP8, Nx15.3, PP Modules
Simatic IPC 427E
1FT7 Motors
AIM, ALM, SMM and DMM
Linear Scale LC 495
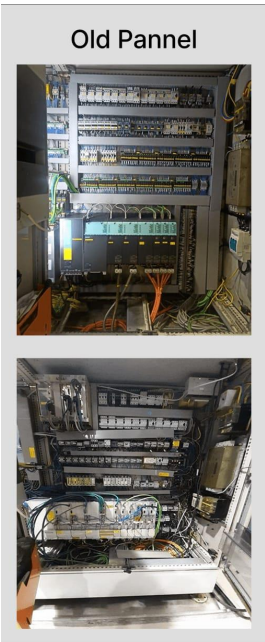
UVA grinding machine
Automation for a proprietary UVATRONICS controller
with no documentation and cost constraints
Project details
Problem Statement
There was no support for the existing Proprietary UVATRONICS
controller.
Many accidents with machines occur due to zero shifting.
There is no reference for the Selection of Automation Components.
Cost constraint while selecting Hardware.
There is no documentation of the machine.
Solution Provided
Selection of Automation components along with required option bits.
Motor Mounting and Field cable routing.
New Panel Wiring.
Machine Configuration, Grinding software 2 channel configuration.
User Intuitive Screens.
Application Prove out.
Machine Details
2 Channel for Parallel operations
Channel X, Z for Bore Operation
Channel2 U, W for Seat Operation
New System Details
828D PPU, SW 280, 2Channel, 4.95, PP Modules
1FT7 Motors
SLM, SMM and DMM
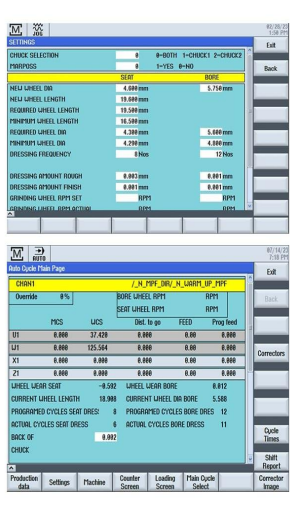